Automatic welding is an important topic, the computer plate screw machine efficiency is very high, non-manual can be compared, the principle is that the solid solder wire is heated by the automatic heating iron melting, at the same time with the flux in the welding metal flow, after cooling to form a solid and reliable solder joint, automatic dispensing machine is widely used in semiconductor, electronic parts, LCD manufacturing and other fields, The process is done by the machine itself, we only need to control the machine manually. When the solder is tin-lead alloy and the welding surface is copper, the solder first wets the welding surface, and with the wetting phenomenon, the solder gradually diffused to the metal copper, forming an adhesion layer on the contact surface of the solder and metal copper, so that the two are firmly combined. Therefore, it can be said that automatic welding is completed by three physical and chemical processes: wetting, diffusion and metallurgy.
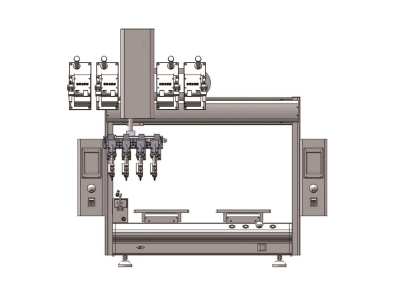
What is the meaning of automatic welding and virtual welding? Solder leakage generally refers to the phenomenon that there is no tin on the pad during the welding process of the automatic soldering machine.
The reasons for this phenomenon are as follows: First, the welding head does not touch the solder joint. At this time, we need to adjust the coordinates of this point, so that the welding head contacts the welding spot, so that there will be no leakage of welding; In one case, the surface of the pad is so oxidized that the tin cannot be glued at all. Virtual welding generally refers to the fact that the solder joint looks OK in the welding process, but in fact the welding is not strong or the amount of tin penetration is not enough. The main reason for this is that the welding head of the automatic welding machine does not stay on the pad for long enough or the temperature is too low. Therefore, we only need to extend the residence time in the welding head or increase the temperature.
The proper and reasonable use of the ability at all times in the welding process is also an important part of the work of welding technology. If it is through the welding of the printed circuit board, it is generally appropriate to 2 ~ 3S. The welding time is too long, the welding flux is completely volatilized, the welding effect is lost, the appearance of the solder joint is oxidized, and the appearance of a solder joint is rough, black, not bright, with burrs or activities and other shortcomings. The welding personnel time is too long, the temperature is too high, and the copper foil of the components or printed circuit boards is simply burned. If the welding time is too short, and can not reach our welding environment temperature, the solder can not be fully melted, affecting the moisture of the flux, easy to form virtual welding.
The amount of tin should be moderate, according to the size of the solder joint requirements to determine the amount of tin immersion active solder machine, so that the solder can meet the toughness of the package welding, forming a suitable size and smooth solder joint. Solder joints do not have more tin, tin is very good, on the contrary, such solder joints are more likely to be soldered and have the potential to weld on top of the pile rather than on top of the pile. If the amount of tin is not enough, you can re-weld, but you must wait until the tin is on the previous melting machine, and then take out the active welding machine; If the amount of tin is too much, the appropriate tin can be removed with the tip.